I’ve been busy making my patterns and jigs for my first scratch build. Mark makes the pattern by cutting in from one side and then removing the waste and exiting the piece of MDF the same way he went in. I had visions of pulling the band saw blade off the pulleys or breaking the blade trying to make the necessary torturous curves and turns. So I took my piece of MDF and cut it in half, clamped the two halves together, marked the required shape then cut out the waste on the two halves - much more accessible. Usual sanding to the lines of the shape was easier too. The two halves were then joined back together using biscuit joints. See the attached photos.
ingenious!
I just use the CNC
😆
Online guitar making courses – guitarmaking.co.uk
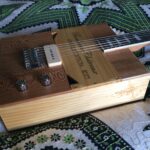
@tv101 CNC eh, hmmm. Surely that takes all the fun, excitement, frustration, blood,sweat, tears, satisfaction (delete as appropriate) out of this wonderful mad journey we’ve embarked upon!!🤣🤣
P.S. I’m only jealous I don’t have a CNC👍🤣🤣
it's just a different sort of fun!
In the old (BCnc) days, I used to spend ages making templates, only for a router to slip first time I used it, and wreck it! This way, I can have a library of templates and just make a new one whenever I need it, or skip the template altogether and cut out the cavities using the machine.
CNC'ing cavities takes a lot longer than using a router - at least the way I've set-up my CNC! I think the answer is a bit of both - CNC the first few mm of the outside of the cavity, just enough to be able to use a bearing guided router cutter for most of it.
Online guitar making courses – guitarmaking.co.uk
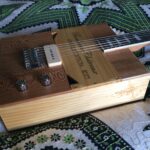
@tv101 Being a poor pensioner, I’m not likely to be able to afford/justify the cost of a CNC and don’t really have the space for one (mind you it would probably fit in the space currently occupied by a Radial arm saw that I hardly use) . Maybe I could sell something to raise the money - something like a kidney!!🤣🤣
I can see the advantages of CNC, labour saving and precision, but unless you’re going to make a load of guitars or put it to other uses it seems like an expensive luxury. Mind you I know a man who knows a man who has one.......nah, that would be getting someone else to do it for me!!🤣🤣
AwRaBest.
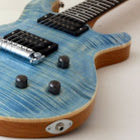
I got lucky and managed to grab a decent s/h CNC from a mate who was upgrading. Without that bit of luck, I'd not have one either.
Mine gets used more for household projects than guitar building. Current project is building a pull-along trolley shape-sorter toy thing for my grand-daughter, with a series of different tops/shapes for her to progress through as she gets older. I'd not even try something like that by hand!
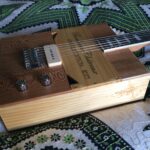
@tv101 Great that you get the most out of your CNC and, yes, it must allow you to do stuff you couldn’t or wouldn’t otherwise attempt.
On a slightly different tack here, most of the routing I’ve done in the past has been jobs I can use my router table for, haven’t done much hand held routing work. I note that Mark in his videos just plunges down into the rout and off he goes, what I’m wondering is if there’s any advantage of drilling a starter hole to the required depth and starting the router with the bit in the hole? Just seems to me that it would put less stress on the machine.
I prefer to drill out the bulk of material with a forstner bit before routing the cavities. With a decent drill press (with good clearance) and a depth stop it saves me from a lot of routing.
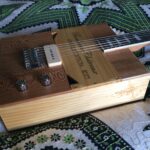
@swepri That’s an approach I’ve used often, usually before clearing out with a chisel e.g. in cutting a mortise. Would definitely reduce the amount of material to be routed out.👍😃