So you recommend minimal carving for the first guitar which makes sense but is the reason for this just because of how likely I’d be to screw out up first time around? As I don’t want a flat top guitar, (the kit one I made is like that and just not a comfortable) I’d plan to have a belly carve, elbow carve and at least the bottom cut away carved. My plan to make sure this goes well was to make a blank from whatever I have, likely pine 😬 and practice the carving on that, presumably it’s be be quicker progress than on the mahogany but should help me nail the techniques? Is this actually that bad of an idea!?
Thanks
…on an elaborate journey to turn trees into music.
@tej I would honestly say that just for your first build, follow the steps in the video course. I know you have ideas (we all do) and you want to build something you don’t have but find your feet first. That old saying my dad always told me, “Don’t try and run before you can walk”. It’s annoying I know and I hate it too but there is truth in it. All of that body carving you have mentioned is done on the course so you will get to do it. Also, I wouldn’t bother with trying to carve pine, just build the guitar and carve the mahogany. It’s a great wood to work, not as hard as you think. Pine is full of resin and will clog up your tools and sandpaper. Just take your time and work that mahogany, just wear a proper dust mask, it’s essential. Good luck man. 👍
Make guitars, not war 🌍✌️🎸
I’d plan to have a belly carve, elbow carve and at least the bottom cut away carved.
Assuming that you're making a solid body with no cap, then those carves shouldn't be difficult to do. Mahogany (depending on what sort it is) isn't usually hard to carve assuming that you've got a suitable tool (eg rasp) for removing the bulk of the material.
Once you've removed the bulk, then it's just a matter of refining and smoothing the curves with sandpaper and/or scrapers until it feels good to you. There is no textbook "right", so you're not aiming for a predefined outcome, just whatever feels good to you. Although there is no "right", there are some "wrongs" ...
If it's a hollowbody or chambered, then just make sure (!) you don't carve through the back when doing the belly carve.
If it's got a cap, then the elbow carve can be a bit trickier, and a drop top might be better - though that's trickier in itself.
But, as with most things in guitar building, go slow, remembering "you can easily take more off, but it's harder to put it back".
And, "if in doubt, have fun".
Online guitar making courses – guitarmaking.co.uk
you can easily take more off, but it's harder to put it back
Pft it’s like you think that saw dust mixed with wood glue doesn’t give a nice finish 😛
I’ve no intention of a top for this first one though, it’ll happen just not this time around. I need to get some rasps/surforms, I’d posted elsewhere and I think someone (possibly you) recommended a few to get. Seem to be a few different profiles available.
Actually while I think about it what’s your experience of different glue? Every video I’ve seen seems to favour Titebond II any idea if there’s a reason for this when it comes to guitar construction or is my trusty bottle of Evo Stick fine?
…on an elaborate journey to turn trees into music.
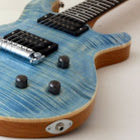
Saw dust and wood glue has saved a few builds for me!!
Re rasps/surforms, I've got one of these;
https://www.axminstertools.com/japanese-two-handed-saw-rasp-200502
and one of these;
https://guitarmaking.co.uk/product/guitar-makers-rasp/
Either are great for bulk removal.
I also like the microplanes which are available in different shapes/sizes. Those are more accurate, for smaller areas and more refined cutting. This sort of thing;
https://www.microplane.com/snapin-8in-flat-set
I've never really liked the round surforms as they always get clogged up and then I never think that they cut as well.
But everyone has their own preference.
I can't really comment on different glues. I've just always used Titebond original (red) for general gluing. If it's good enough for Mark and all the guitars that he's built (and good enough for my cabinet maker friend and all the cabinets that he's built) ...
I rather like the idea of having some nice hand tools and taking my time carving a top.
But if you want to get the job done quickly, and you don't mind noise and LOTS of sawdust, these are the way
The easiest way to carve a top or hollow underside is to use gouges with a fairly flat curve because you can remove a lot of material in one go and it makes chips rather than dust which is better all round. Start from the edge usually and work in to avoid splitting, although it depends on the grain.
Traditional method is to make holes in the wood using a drill set to a depth needed to reflect the desired curve, then join up the holes. Allow for the tip or Brad point and when you’ve reached the mark it’s time to stop. Obviously leave a bit extra for sanding or scraping.
Some of the big makers use a copy router or CNC machine to get to this stage before final hand finishing. Pfeil gouges are a good make to use, razor sharp from the start and can be struck with a mallet which saves blisters.
l’ve found that rasps and surforms are ok for solid wood shaping but not where the final thickness is critical, but that’s only my experience. Other people may prefer them.
Some people call me a tool, others are less complimentary. Tools being useful things.
Mark uses ordinary white glue for some jobs and he did say on a live stream that it’s a good option but takes longer to set before handling, overnight as opposed to 30 minutes for Titebond. If your not confident about glue joints and think you might have to take it apart and try again, use white glue. It softens with moderate heat, whereas Titebond is much more difficult to get apart. Both are stronger than the wood. If your Evostick has been in an outside workshop over the winter buy a new one as it doesn’t like freezing temperature.
Some people call me a tool, others are less complimentary. Tools being useful things.